"Fixed tool TP processing" for complex shaped lightweight structures in an integral design
This research aims to improve and facilitate the manufacturing of thermoplastic FRP structures. Based on unique semi-material properties, simpler tools may be used to manufacture complex structures with an integral design.
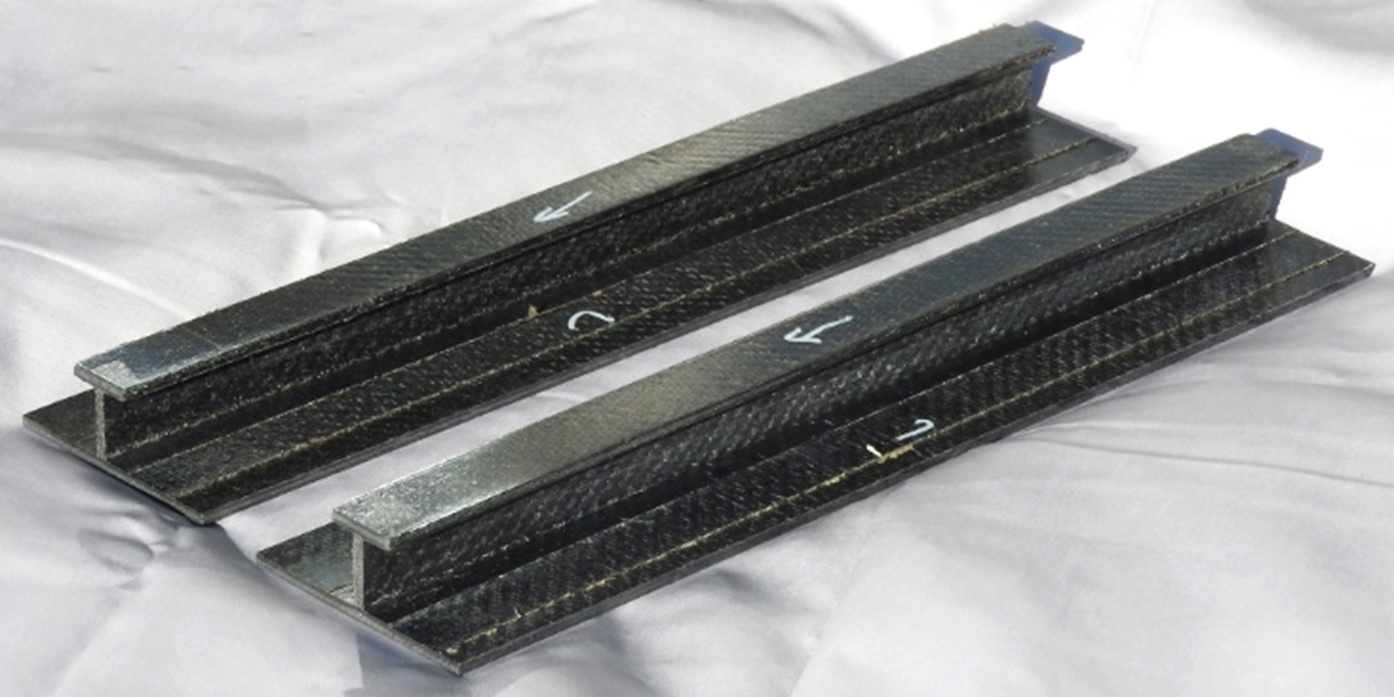
Project team
- Lukas Spirig (inspire AG)
- Dr. Markus Zogg (inspire AG)
- Burak Baser (Mitsubishi Chemical Advanced Materials AG)
- Kevin Papierok (Mitsubishi Chemical Advanced Materials AG)
Project Duration
November 2021 to present
Funding
- Innosuisse Project 55029.1 IP-ENG
Project description
The majority of today's high performance FRP structures is made of carbon fibre reinforced epoxy resins in an autoclave process. However, for further improvements in automation, material toughness and good burning resistance it would be beneficial to use high temperature thermoplastic matrix systems like PEI or PEEK. The current drawback is that for the required processing temperatures of these thermoplastic matrix systems (> 320 °C) no cost efficient auxiliary materials (e.g. vacuum bags) are available. Therefore, today mainly complex full metal tools with sliding mechanisms are used to manufacture simple thermoplastic FRP parts. If required, these parts are then joined (e.g. by welding) in a second manufacturing step.
This research project with Inspire AG and Mitsubishi Chemical Advanced Materials AG aims to investigate a novel manufacturing method for thermoplastic FRP parts that enables simpler tools. The approach is based on a material that creates an internal pressure during manufacturing and therewith generates the required pressure to manufacture high-quality FRP parts. Because of the pressure from the material, no sliding mechanism is required on the tool. This leads to significantly simplified tooling compared to classical thermoplastic FRP composite processing. Therefore, complex composite structures can be manufactured in an integral design.
The scientific targets of this project are to quantify the mechanical performance of these materials and to identify best lightweight structures that use an integral design by "fixed tool thermoplastic processing". The potential of the novel approach is shown on different demonstrator parts; the target applications are the automotive and aerospace industry.
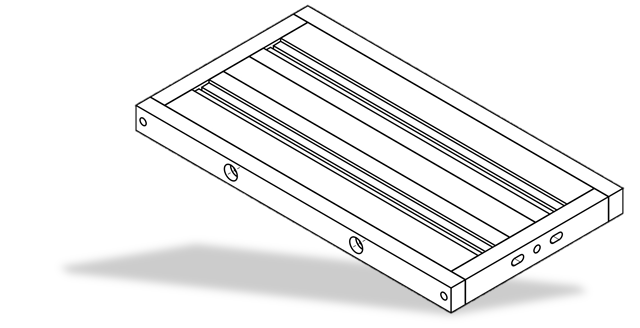